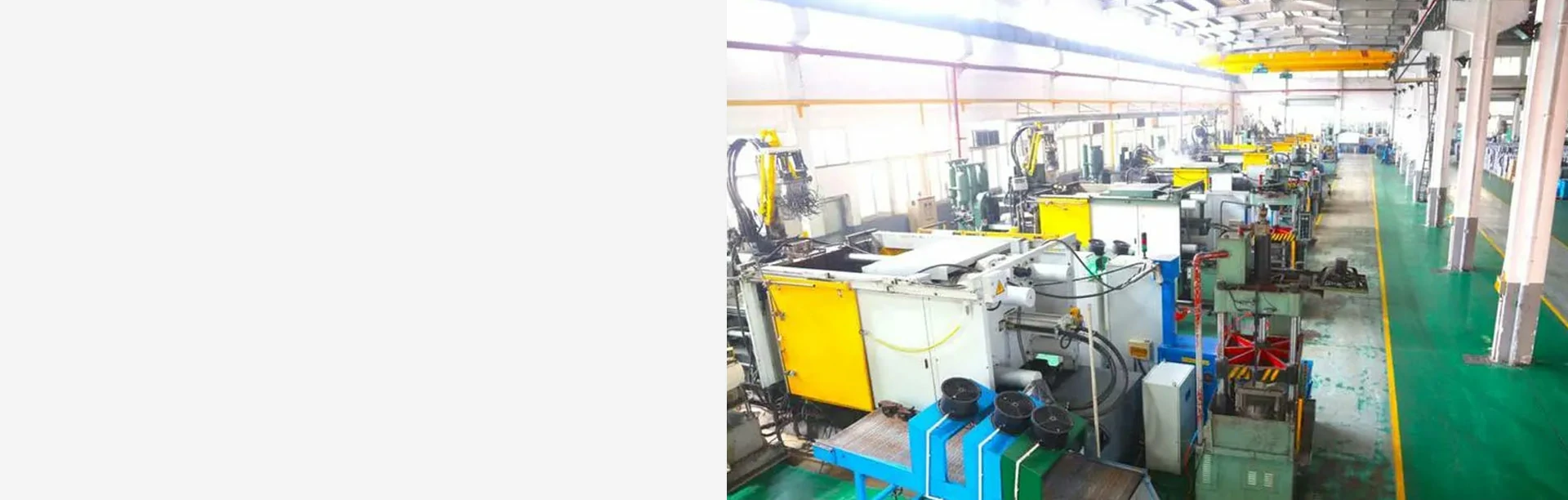
Zinc Die Casting
We produce zinc die casting parts from a few grams to more than 50 kg with superior quality ready for assembly.Main capabilities can be breakdown as below:
- Die Casting Zinc Alloy: ZAMAK 2,ZAMAK 3,ZAMAK 5,ZA 8
- Die Casting Mold Material: H13, NAK55, NAK80, SDK61, S136, LKM2344, LKM718, etc
- Mold Base Brand: LKM(China), DME, EMP, Hasco, MISUMI
- Mold Life: 80,000~150,000 shots
- Tolerance Standard: +/-0.005mm
- Part Weight: 30 gram~50KG
- Die Casting Machine Tonage: 30T-128T-280T-550T
What Is Zinc Die Casting – Zinc Alloy Die Casting Define
Zinc alloy is an alloy composed of other elements based on zinc. The alloying elements that are often added are aluminum, copper, magnesium, cadmium, lead, and titanium. Zinc alloy has low melting point, good fluidity, easy fusion welding, brazing and plastic processing, corrosion resistance in the atmosphere, easy recycling and remelting of residual waste, but low creep strength, prone to natural aging and dimensional changes. Prepared by melting, die casting or pressure processing. Zinc alloys can be divided into cast zinc alloys and deformed zinc alloys according to the manufacturing process. Cast zinc alloy has good fluidity and corrosion resistance, and is suitable for die-casting instruments, automobile parts casings, etc.
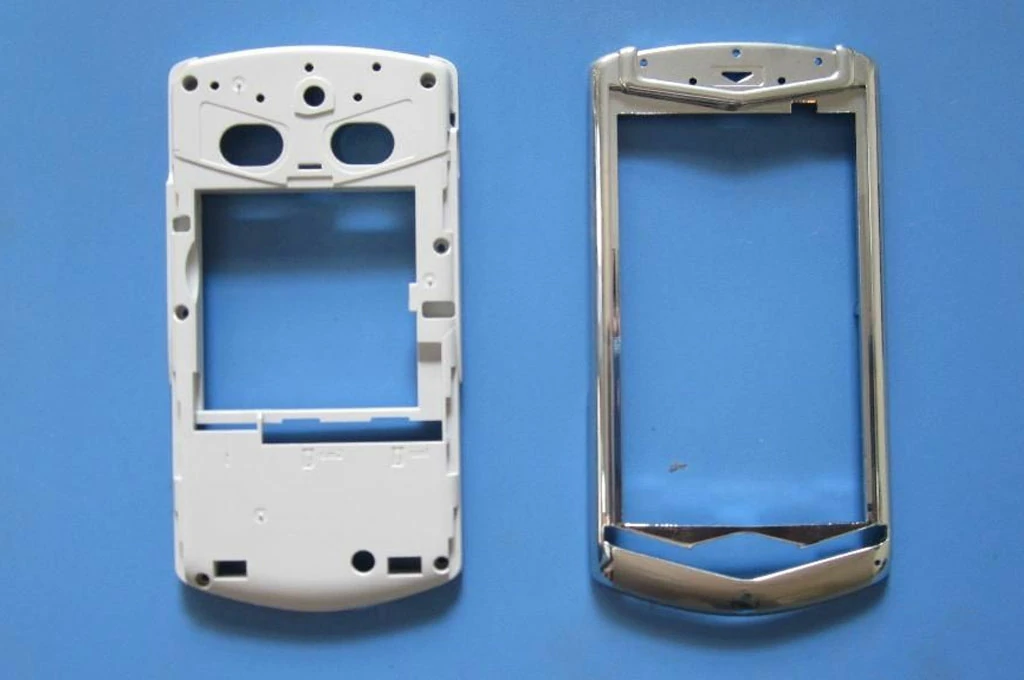
Zinc alloy die-casting is a precision casting method that uses high pressure to force the molten zinc alloy into a complex-shaped zinc alloy die-casting mold. Zinc alloy die casting is no better than other molding technology. If you want to make good die-casting products, not only you should have a good die-casting machine, but also combine the mold, die-casting machine and die-casting process to make a good product.
Except for those containing iron, most alloys are suitable for die casting. Different alloys have different physical and mechanical properties, providing a wide range of product designs. Aluminum and zinc alloys are the most commonly used materials for die casting, followed by magnesium, zinc-aluminum, copper, tin and lead alloys. Zinc alloys have always maintained an important position in hot chamber die casting due to their good die casting properties and mechanical properties.
The advantages of zinc alloy are low melting point, convenient melting and heat preservation, less heating of the pressure chamber and die-casting mold wall, prolonging the service life of the mold; good casting performance; no iron absorption during melting and die-casting, and it is not easy to stick to the film; there is a good Mechanical properties and abrasion resistance at room temperature, excellent impact resistance, are widely used in die casting different products, especially thin shell products and products with smooth surface for electroplating and painting.Zinc die castings are applied in contexts throughout industry, commerce and even in consumer products contexts such as Machinery and Auto industries.
How To Make Zinc Die Casting
Die casting is to pour liquid or semi-solid metal into the pressure chamber of the die casting machine. Under the action of the moving injection punch, the molten metal fills the cavity at a very fast speed, and crystallizes and solidifies under the action of pressure to obtain the casting. a way. First of all, the mold is installed on the mold base and tested on the machine; feeding, die-casting, cooling, forming, demoulding, zinc alloy die-casting is a special casting method that develops rapidly in modern metal processing technology. It is the process of filling the mold with molten metal under high pressure and high speed, and crystallizing and solidifying under high pressure to form a casting. High pressure and high speed are the main features of pressure casting. The commonly used pressure is tens of MPa, the filling speed (gate speed) is about 16-80 m/s, and the time for the molten metal to fill the mold cavity is extremely short, about 0.01-0.2 seconds.
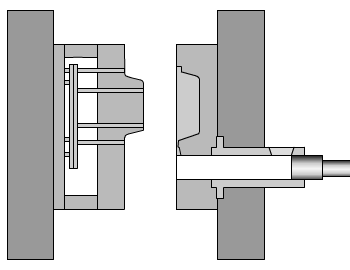
Zinc Die Casting Service In China – Leading Zinc Alloy Die Casting Parts Manufacturer
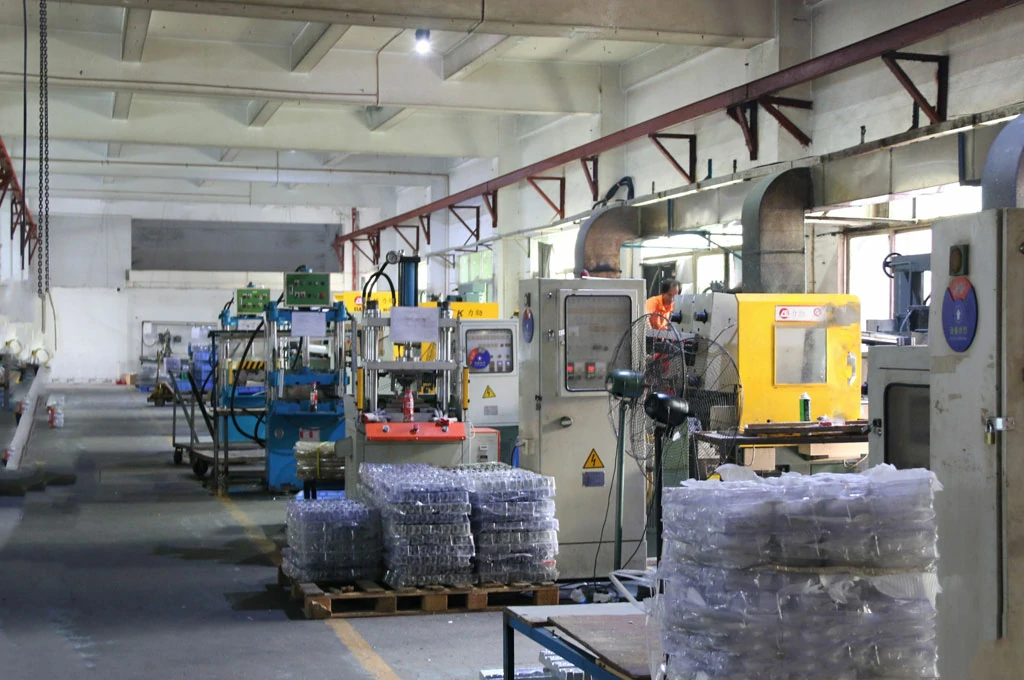
If you are seeking a professional zinc die casting supplier to provide high quality precision zinc die casting parts,Pintejin is one of the most affordable and capable manufacturer, specializing in high pressure casting process on advanced 30T-128T-280T-550T zinc die casting machines. Pintejin offer a broad range of zinc die casting surface finishing including powder coating, e-coating, shot blasting, chrome plating, and bright finish. The industries Pintejin serves include automotive, food dairy, machinery, medical, plumbing, watering, mining, petrochemical, electrical, energy, aerospace and others.You have a complex part design, Pintejin Zinc Die Casting Company can help you turn it into a reality. With the right equipment, strong technical knowledge, and a focus on quality.. From tool design to finishing and then on to shipment, Pintejin ensure that every project is completed to a high standard and that your orders are delivered on time, every time.
CNC Machining Zinc Die Castings services
Pintejin offers close-tolerance CNC machining including turning, milling, drilling, boring, and tapping capabilities. With the ability to produce both high-quality zinc die cast manufacturing and CNC machining services, Pintejin is your one-stop-shop for zinc alloy die casting and machining. We own advanced techniques, professional engineering team and modern die caster to ensure that the zinc die casting parts meet your requirements and achieve the demands for precision and productivity. Our zinc builder will manufacture the appropriate zinc die castings for you for cold chamber die casting machines with a maximum of 550 tons closing force.
The Material Information Of Zinc Die Casting
Reasonable selection of zinc alloy materials and correct disposal of waste materials to strictly control the content of impurity elements will help prevent poor control of alloy composition, resulting in excessive impurity content in castings, resulting in cracking of castings due to intergranular corrosion, affecting the mechanical properties of castings. The zinc alloy die-casting materials we often do are:
- ZAMAK 2:Tensile Strength (Mpa):359;Thermal Conductivity (W/mK):105;ZAMAK 2 Has Excellent damping capacity,High strength,hardness levels after long-term aging and vibration attenuation.Its Superior to other Zamak alloys with creep performance.
- ZAMAK 3:Tensile Strength (Mpa):283;Thermal Conductivity (W/mK):113;ZAMAK 3 Has Great balance of physical and mechanical properties,Good castability and long-term dimensional stability,Good damping capacity and vibration attenuation and Excellent finishing characteristics for plating, painting, and chromate treatments.
- ZAMAK 5:Tensile Strength (Mpa):328;Thermal Conductivity (W/mK):109;Zamak 5 Has a higher copper content than Zamak 3, which results in higher strength.It Has less ductility than Zamak 3.More readily plated, finished, and machined than Zamak 3.
- ZA 8:Tensile Strength (Mpa):374;Thermal Conductivity (W/mK):115;ZA 8 Ideal for decorative application.It has excellent finishing and plating characteristics,Good performance of strength, hardness, and creep properties.
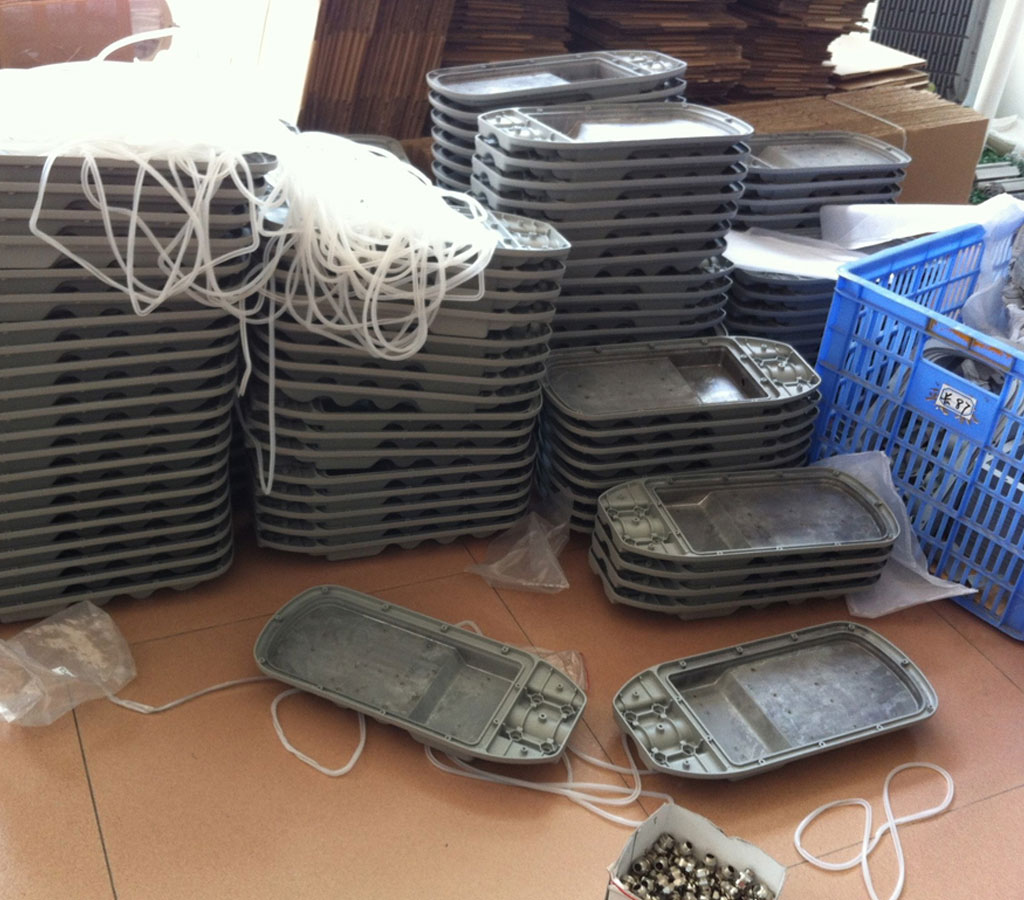
Related Guide Of Zinc Die Casting
How To Choose Right Zinc Die Casting Machine
Die-casting machine is the key equipment of die-casting production, and its performance determines the quality of die-casting parts objectively. The correct choice of die casting machine is crucial to ensuring product quality, improving production efficiency, reducing production costs and ensuring production safety. The performance of the die casting machine mainly depends on the following two aspects:
- Sufficient clamping force: It helps to prevent burrs from appearing when the metal melt pressure is at the highest peak, and at the same time has the resistance to breakage to avoid flying materials during die casting. "Zhuzun" die casting machine specially designed five The point double-hinge clamping structure has sufficient clamping force. For example, when the %&” machine only uses the system pressure of ‘#( in the national technical supervision and spot check, the measured clamping force reaches ")#$&*. sufficient clamping force.
- Sufficient injection capacity: to ensure that die casting will not cause overheating of the mold or a large amount of overflow, and at the same time to ensure that the machine has sufficient capacity to deliver enough molten metal and fill the mold with the required high ingest speed in a short time. cavity. The maximum air injection speed of "Zhuzun" die-casting machine is ,-./, and the injection ratio is large, which can die-cast any required zinc alloy products.
Advanced functions, easy operation, reasonable price and complete specifications are the characteristics of "excellent" die-casting machines. After choosing a die-casting machine brand that can meet the needs, it is particularly important to choose a die-casting machine with appropriate specifications. On the one hand, it can be selected according to the size, weight and complexity of the shape of the product (whether core pulling is required); system) to calculate the bulging force to select a die-casting machine with a slightly larger clamping force. Some small die-casting parts, such as buttons, pouch hooks, zipper pullers and lighter accessories, can be made into multiple molds in one mold; another example is the combination mold used by some customers for watch case production, and CM55 is used for one mold with four sets of combination molds Or CM88 die-casting machine is the most suitable, instead of using large-sized machines with small molds and small products. It cannot be unilaterally considered that a machine with a large tonnage (large clamping force) means high pressure. On the contrary, the small area of the mold will cause the pressure to concentrate in the middle of the large template, causing damage to the die-casting machine template and mold, and also causing waste of resources, which does not meet the requirements of environmental protection.
The Design Of Zinc Die Casting Die And Runner System
Since the zinc alloy must fill the cavity within 0.02-0.04 seconds, the design and manufacture of the die-casting mold and its runner system is much more demanding than that of the plastic mold. The runner system is to guide the molten metal to fill the cavity in a certain way. It plays an important role in controlling and regulating the flow direction, pressure transfer, filling time, exhaust conditions and mold temperature distribution of the molten metal, and also determines the die casting. An important factor in the surface quality and internal quality of parts. However, many manufacturers are used to making die-casting molds by making plastic molds. As a result, the die-casting machine must be produced with high pressure, high speed, high temperature and increased clamping force, resulting in defects such as air bubbles, cold insulation and shrinkage holes. , The runner returns to the furnace, the yield is low, and the energy consumption is large. In order to obtain high-quality die-casting parts and achieve maximum die-casting efficiency, an excellent runner system must be designed. This system makes the flow of molten metal in the cavity smooth, minimizes pressure loss, and allows the remaining air to be discharged smoothly. Produce high-quality castings in the most economical way.
- The metal runner system is composed of a series of pipes of different lengths and diameters, which bring the zinc alloy melt from the lower side of the injection plunger to the gate at different high speeds. In addition to the changes in length and diameter, there are also many directions. Each change requires energy consumption to overcome resistance, so the design principle of the runner system should converge from the gooseneck to the gate, avoid sharp corners, and smooth the surface of the flow path to reduce resistance and maintain Flow velocity of liquid zinc alloys.
- Use a conical inlet with a sprue.
- The main runner adopts an ideal runner-type runner design. The cross-sectional area of different runners in the runner gradually decreases toward the flow direction, and the corners are elliptical curves, that is, the bend should have a larger The purpose of the bend radius is to reduce drag and reduce the possibility of trapped air and cavitation in the bends downstream of the runner.
- Try to use long tapered tangential runners and thin gates. The flow rate at the gate is ideal for 40-60 seconds.
- Minimize overflow (garbage level) settings as much as possible, and select suitable exhaust ducts.
- Good thermal balance between cavity, wall thickness and temperature.
Smelting Zinc Alloy Correctly
What Are The Advantages Of Our Zinc Die Casting Services?
- All of our zinc die castings are guaranteed to be shipped to you on time.
- Our staff is dedicated to providing the highest levels of customer service to ensure full customer satisfaction every time.
- Our die casting zinc alloy is ideal for those project requiring complex shapes or unique requirements.
- Our zinc die castings are of the highest quality and most affordable prices.
- Finish the parts in time to provide the strongest support for your R&D projects.
- Do zinc die casting manufacturing according to your drawings or samples
- We offer customers full-service zinc alloy die castings and related capabilities from design to delivery. We work with a large variety of metal options, making us your one-stop source.
Benefits of Zinc Die Casting
- It’s bigger than weight, has more texture than weight, and has more strength than plastic injection molding.
- Good casting performance, can die-casting complex shape, thin-walled precision parts, casting surface is smooth.
- Surface treatment: electroplating, spraying and painting.
- No iron absorption, no corrosion, no die sticking during melting and die casting.
- Good room temperature mechanical properties and wear resistance.
- Low melting point, melting at 385 ℃, easier to form than aluminum alloy die casting
Zinc Surface Finishing In Pintejin Zinc Die Casting Company
Our zinc surface finishing includes (but is not limited to):
- Powder Coating (electrostatic application)
- Wet Paint
- Chromate
- E-Coat
- Electroless Nickel
- Chrome
- Silk Screening and Stenciling
- EMI/RFI Shielding
- Surface Conditioning (shot and bead blasting)
The Features Of Zinc Die Casting Parts
- Good strength and hardness
- Good casting performance, can be used for casting precision parts with complex shape and thin wall, and the casting surface is smooth.
- Surface treatment: electroplating, spraying and painting.
- During melting and die casting, no iron absorption, no corrosion, no mold sticking.
- High dimensional accuracy and stability.
- It has good room temperature mechanical properties and wear resistance
- Low melting point, melting at 385 ℃, it is easier to form than aluminum alloy die casting.
The Method For Controlling Zinc Alloy Die Casting Defective Rate
- To control the generation of pores, the key is to reduce the amount of gas mixed into the casting. The ideal metal flow should be continuously accelerated from the nozzle to enter the cavity through the shunt cone and the runner to form a smooth and consistent metal flow. The design of the runner, that is, the pouring flow should be gradually reduced from the nozzle to the inner gate at an accelerated rate, which can achieve this purpose. In the filling system, the mixed gas is due to the mixing of turbulent flow with the metal liquid phase to form pores. From the study of the simulated die-casting process in which the metal liquid enters the cavity from the casting system, it is obvious that the sharp transition in the runner and the incremental pouring The cross-sectional area of the runner will cause the molten metal to flow turbulently and entrain the gas. The stable molten metal is conducive to the gas entering the overflow groove and the exhaust groove from the runner and the cavity, and then being discharged out of the mold.
- Die-casting is the final product of die-casting production. The design of die-casting is the first job encountered in die-casting production technology. Zinc alloy die-casting is mainly designed according to the requirements of use. Whether the structural process of die-casting is reasonable? The structure, the quality of the die casting, and the production cost have a direct impact. If the structure of the zinc alloy die casting is unreasonable, it will not only lead to a complex mold structure, but also cannot guarantee the molding quality. For hot cracks: Do not change the thickness of the die casting sharply to reduce stress; adjust the relevant die casting process parameters; reduce the mold temperature.
- For the phenomenon of intergranular corrosion: mainly control the content of harmful impurities in alloy raw materials, especially lead <0.003%. Pay attention to the impurity elements brought by the waste.
- For water marks and cold insulation, the mold temperature can be increased, the gate speed can be increased, or the overflow groove can be enlarged in the cold insulation area to reduce the appearance of cold insulation.
- The manufacturability of zinc alloy die castings refers to the applicability of die castings to forming and processing. The shape, structure and size of die castings directly determine the specific structure and complexity of the die casting mold. We should try our best to design the mold. It is simple, reasonable and feasible. Therefore, compared with die-casting parts, it is required to achieve reasonable structure and beautiful appearance in combination with the needs of die-casting molds without affecting the structural function, aesthetics and performance of die-casting parts. Easy to manufacture.
- In addition to the influence of various technological factors on the quality of die castings, the craftsmanship of the structural design of the parts is also a very important factor. The rationality of the structure and the adaptability of the process determine whether the follow-up work can be carried out smoothly. Various problems encountered in die-casting production technology, such as the selection of parting surface, runner design, and precision requirements, are all related to the die-casting process of the die-casting itself.
The Application Of Zinc Alloy Die Casting
- High precision requirements such as: electronic equipment shell, mobile phone shell, U disk shell, other accessories with high precision requirements, etc.
- Craft gift industry: such as badges, medals, trophies, keychains, bottle openers, metal ornaments, medals, power, etc.
- Luggage and clothing hardware: buttons, hook buckles, belt buckles, rope buckles, stretch buckles, carabiner, etc.
- Other accessories such as: liquor license, hinge, bottle cap, smart door lock, massager shell, etc.
Why your price is more reasonable then other china supplier?
- 1.the material of die casting: Lee KEE Group aluminium & zinc and etc
- 2. Die Casting machine:LK GROUP , YIZHIMI Group,lijie
- 3.Use Green Energy ,Save the world : Huawei,Natural gas,Electricity ——choose us , for the Minghe Casting.thanks
- 4, Die Casting Mold :Bigger Size ,and more than 50000 shots mold life.
- 5.Inspection equipment:CMM
Anodizing Zinc Alloy Parts In China Copper-Plated Zinc Alloy Jewelry By Die Casting Furniture Hardware Zinc Die Casting Parts led Small Spotlight Housing By Zinc Die Casting Zinc Alloy Die Casting Barrel Parts Zinc Alloy IPC Enclosure Zinc Alloy Phone Case Zinc Die Casting Custom Building Parts Zinc Die Casting Custom Metal Ring Zinc Die Casting Kitchenware Parts Zinc Die Casting Lock Button Parts Zinc#8 Alloy Die Casting Parts