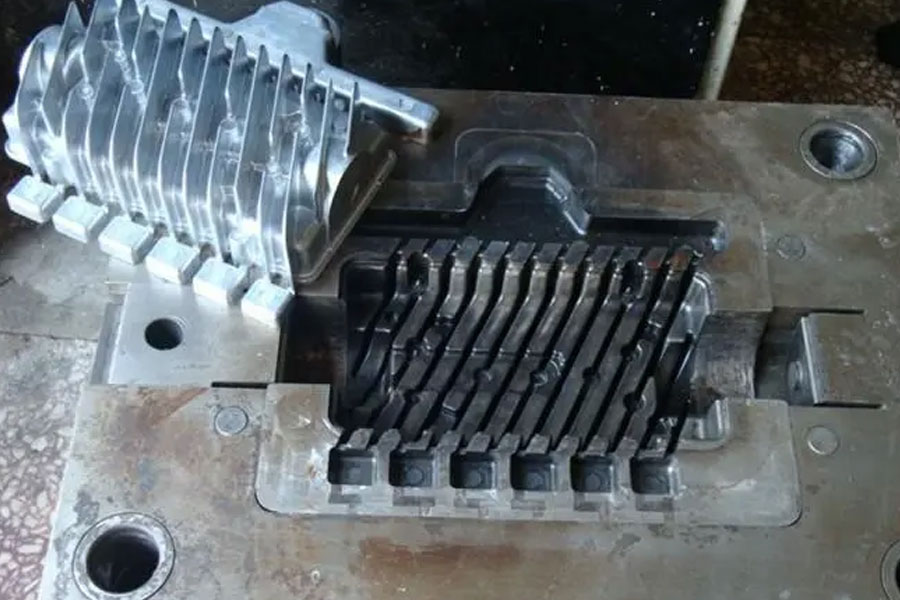
A lot of information about the gate of die-casting molds can be consulted. The research on die-casting began in the 1920s. This is a common question, but after decades of development, from experience to theory, to the introduction of foreign advanced concepts, there are already relatively mature casting systems in China. Of course, each company has unique insights. and experience, but always the same. Below I will briefly talk about my personal understanding of the gating system.
To start with this topic, in fact, there are still many considerations for the pre-production of the gating system, such as product information, alloy composition, the use of the parts, and the performance and technology of the die-casting machine with this gating system, etc. The series of questions will not be introduced one by one here, and we will wait for the publication of subsequent articles.
Die casting is always a contradiction, so many friends may be puzzled, but why do you say this?
First of all, die-casting has evolved from processes such as sand-casting, but the parts produced by sand-casting and other processes have completely opposite effects. Many friends say that I can cast and die-casting is no problem. I think that although it is an extension of the former, the two are integrated into one, and the future research and development directions are also in their own directions, but in the end they reach the same goal. Only by understanding the direction of the bifurcation can we integrate for the final return. Secondly, die casting does not require a separate process and mold design. As I said earlier, all aspects are involved here. But everyone remembers that die-casting is a matter of optimization, because the requirements for the parts we target are different, and we can only take care of one and lose the other. Many friends say that I have done this type of die casting, but I don’t agree with it very much here, because as long as the parts change slightly, the direction we consider will also change, such as the problem of the parts process, 2 outbreaks, etc. It will be accompanied by quality problems. At most, it can only be said that there is experience, but this experience is not optimal.
1. Flow problem: When it comes to the pouring system, we will first think of the inner gate.
The inner gate refers to the narrow area of the die-casting liquid from the runner to the product. This area is the most critical to the quality of our parts. So what is the best cross-sectional area of the ingate? Everyone has many methods and experiences, but the best is the flow method. See the formula below:
- (V piece + V row) / time * speed
- (G piece + G row) / density * time * speed
I believe that you can find these two formulas if you find any information. I will briefly introduce them here, that is, the weight of the product plus the weight of the slag bag divided by the density of the product, divided by the filling time of the product, divided by the filling speed of the product, which can be divided evenly. . Everyone understands this principle, but many people often cannot grasp the time and speed of many materials. In fact, no matter from the flow method or the PQ square, a lot of data can be determined, but the time and speed are still controlled by our human experience, which brings us some trouble. As shown in the figure:
As shown in the figure, the position of the window is determined by time and speed, and this time and speed are given by our experience, so the real meaning of this is to master time and speed. Many data are too large in terms of time and speed, which often results in too large deviations in the calculated data.
As shown in the figure:
If you follow this table, then our flow method is simply useless. Here I simply use 2 methods to tell you the simple method.
(G piece + G row)/2.5*0.05*40
2.5 is of course the density of molten aluminum, and the weight of parts and slag bags is in grams. Here we should note that in the filling state at this time, the density should be calculated according to the liquid density. This formula is suitable for aluminum alloys with a wall thickness of 3-6 mm, and most of the alloy parts we contact are often within this range. Because the flow rate is too large, the gas content of the product tends to increase. Although the process can better meet the high-speed and high-pressure process, once the time is too short, the gas in the cavity does not have enough time to be removed, and the gas content of the product will inevitably increase. If the filling time is long, then we often see a series of problems such as cold isolation, blackening, looseness and even cracking of the product when the mold is opened. Therefore, in terms of appearance parts or airtight parts, the filling time of the product is particularly important. The second method can basically make 27%-30% of the weight of the product to calculate the cross-sectional area of the inner gate required by the product. The former is used for thick-walled parts, and the latter is used for thin-walled parts, with 3 mm as the boundary. Using these two methods to determine the inner gate range, we can make fine adjustments on the die casting machine for a slight gap. Here is just a brief description of the practical calculation and judgment method of the inner gate. It does not explain the mold material coefficient and the range of liquid-solid phase in detail. If you want to answer the ins and outs in detail, I believe you need to write a book, which is not suitable for our die-casters. method of processing.
2. Flow direction problem: If the cross-sectional area of the inner gate is to meet the flow rate, then the gate is to determine the flow direction of the alloy liquid, and the extension of the runner is also to meet the flow direction of the alloy liquid. Gate refers to the transition area between the inner gate and the runner. It is generally divided into fan gate and conical gate. We have time to explain the area calculation of gate in detail later. Here we mainly talk about Let’s take a look at the orientation problem. In fact, the flow direction is also a crucial issue. Generally, we determine the location of the gate according to the product. Then the problem comes. Generally, the basic appearance of the parts directly connected to the gate, including the density, is ideal, while the location farther away is relatively poor. . It is mainly concerned with the main filling area and the non-filling area. Generally, the main filling area is the area near the gate or in the same direction. The non-main filling area is called the extrusion area. If there is enough product placement, it is best to have the main fill area occupy 2/3 of the product. (The 2/3 here refers to the product flow area, not the gate area). Of course, each part is different, which requires us to judge more accurately. Here are a few main methods:
- Under normal circumstances, try to make the product feed synchronously.
- Try to keep as many direct filling areas as possible.
- Select the position of the gate according to the requirements of the parts. The dense parts are solidified layer by layer or sequentially to minimize the shrinkage of the product, and to disperse the pores in the product as much as possible, so as to achieve the best quality of the product. Packing problem. As shown in the figure:Of course, in some products, we need to pay special attention, that is, the thickness changes more and more, the fluctuation is unstable, and when the fluctuation is 4 times or higher, we cannot blindly consider the method of gate feeding, because these areas No matter how you feed, it will be useless, then you need to consider other methods, such as the control of material temperature, the control of cooling mold temperature or the control of the sequential difference between the flow direction and the cooling and heating of the material temperature, or adding local pressurization, What’s more, processes such as die-casting, die-forging, and semi-solid are considered. The latter is more difficult, and has exceeded our pre-judgment of the product in the early stage, and needs to be judged by means of simulation. Therefore, when developing a product, the best thing is that the wall thickness is uniform, and the thickness difference should be controlled within 2 times as much as possible, so as to reduce the area where the product has two outbreaks. The thickness of the product is generally about 4 mm, the tensile strength and plastic deformation are the best, and it is not easy to generate shrinkage holes. The tensile strength decreases gradually as the thickness of the product increases.
- Select the position of the gate according to the requirements of the parts, and the appearance parts should be synchronously solidified to minimize the deformation of the product, or the defects such as cold cracks and strains caused by deformation stress. As shown in the figure:
- Try to avoid impacting the obstruction area of the product, the flow direction should be stable, and keep the flow direction given by the original gate as much as possible. Generally, the flow direction of the alloy liquid will change after being hit by the cavity. Dead flow and dead flow are the biggest taboos in our die casting and mold design. Once the flow of alloy liquid is discontinuous or there is not enough energy to drive the flow after impact, it will be easier for air shrinkage holes, including butt cold insulation, cold material and other series of defects. produce. The shape of the product is out of our control, but we can avoid it as much as possible. In addition to changing the flow direction, the blindly impacted area will also cause the mold to be eroded, pitted, and cracked in the early stage.
- The process of the product should be controlled as much as possible between the process and the wall thickness ratio of 100-150. Take the former for thin-walled parts and the latter for thick-walled parts.
- When the gate area of the product is sufficient and the shape changes little, the number of gates should be reduced as much as possible. If it is a fan gate, the width of a single gate should not exceed 80mm and the angle should be less than 90 degrees. Try not to impact the exhaust area of the workpiece. The reason is very simple. Once the exhaust is sealed, if the inside of the workpiece is still flowing, then the product is defective.
Hi, this is a comment.
To get started with moderating, editing, and deleting comments, please visit the Comments screen in the dashboard.
Commenter avatars come from Gravatar.